Exemplo de motor Diesel de última geração: o de três cilindros da BMW
Pode-se usar a estratégia de injetar o combustível (ou mesmo realizar a ignição, no caso de motores Otto) durante a fase de compressão, para que a queima ocorra de forma mais eficiente na fase de combustão. No entanto, há um limite físico para esse artifício e, quanto maior for o cilindro, de mais tempo a frente de chama necessitará para percorrer toda a câmara de combustão. Por isso chegou-se a usarem motores na Fórmula 1 com 12 cilindros e cilindrada de 3,0 litros (250 cm³ por cilindro), para que pudessem girar a 18.000 rpm e produzir mais potência (lembre-se da fórmula P = T * rpm, ou potência é igual torque vezes rotação).
Entende-se assim por que é comum um motor Diesel, aplicado a veículos de passeio, obter muito mais torque (com ajuda do turbo), mas potência mais baixa, que no motor a gasolina de mesma cilindrada. Essa vantagem de torque em baixas e médias rotações traz uma maior sensação de desempenho ao motorista. Para melhor entendimento, vamos a gráficos de comparação entre motores Diesel e a gasolina com valores próximos de potência máxima.
Como se pode ver, o torque máximo é bem mais alto no motor Diesel, além de obtido em faixas de rotações mais baixas. Contudo, ambos os motores alcançam potências máximas parecidas, conforme o gráfico abaixo.
Apesar das potências semelhantes (161 cv no Diesel, 152 cv na unidade a gasolina), o Diesel fornece a sensação de desempenho muito superior no uso urbano, pois produz muito mais torque e potência nas faixas mais usadas no dia a dia. Como exemplo, a 2.500 rpm o motor a gasolina tem pouco menos de 75 cv, enquanto o a Diesel já produz cerca de 140 cv. Essa diferença — quase o dobro — traz muito mais agilidade no trânsito ou numa ultrapassagem na qual não seja usada a faixa superior de rotações.
O método carga e o Diesel
Os leitores habituais do Best Cars conhecem o método carga, como chamamos a forma de dirigir que emprega maior abertura de acelerador (carga) e menor rotação para obter o desempenho desejado. Esse método seria válido ao motor Diesel?
Em teoria, sim: por trabalhar sempre com excesso de ar e não ter problemas com detonação, quanto maior a carga (solicitação de torque), maior será a eficiência global do motor. Na prática, porém, tudo depende da situação e da estratégia empregada pelo fabricante. Em alguns casos necessita-se de grande percentual de recirculação de gases (EGR), sobretudo em cargas altas, para reduzir os níveis de óxidos de nitrogênio (NOx — saiba mais no artigo sobre emissões).
No mesmo modelo, em rodovia, o motor Diesel rende por volta de 20% a mais por litro de combustível que um similar a gasolina
Em geral essas regiões de uso do motor não são frequentadas durante os testes-padrão de emissões. Alguns fabricantes então aproveitam essa brecha para não usar EGR nessas situações — afinal, como podem calibrar algo se não houver um limite determinado? Em regra, porém, o método carga pode ser aplicado ao Diesel e trazer boa redução no consumo de combustível. Alguns veículos modernos equipados com transmissão automática têm adotado esse método na calibração da caixa.
Por não haver problema de detonação no motor Diesel, pode-se perseguir sempre o melhor tempo de queima do combustível em cada situação. Já o motor a gasolina pode não estar em seu melhor ponto de ignição para evitar a detonação, o que impacta no rendimento do motor (claro que outros fatores podem influenciar na diferença de rendimento, mas este pode ser considerado o principal motivo).
Para os mesmos motores citados acima, podem ser comparados também os gráficos de consumo específico (medido em gramas por kW a cada hora ou gramas por cv a cada hora) em plena carga, ou seja, com máximo torque:
Nota-se que o motor Diesel obtém consumo específico em média 30% menor. Voltando aos gráficos de potência e torque, vemos que o motor a gasolina produz 75 cv a 2.500 rpm. Após algumas contas, obtemos que nessa condição aquele motor consome cerca de 20 litros por hora, enquanto o motor Diesel produz a mesma potência a 1.500 rpm consumindo em torno de 14 l/h. Vale lembrar que consideramos as curvas em condição de máxima carga (torque), na qual o motor a gasolina tem a grande desvantagem de trabalhar com mistura rica, o que aumenta o consumo (leia em artigo anterior sobre motores).
De posse dos dados em cargas parciais, poderíamos comparar o consumo do mesmo modelo, trafegando em rodovia, com o motor Diesel e outro a gasolina. Em média, com os motores atuais, tem-se uma vantagem por volta de 20% para o motor Diesel nessa condição, na qual o motor a gasolina estaria trabalhando com lambda 1.
Mas como injetar diesel na câmara de combustão na quantidade e no tempo certos?
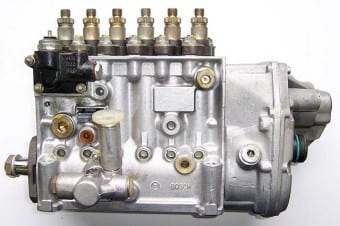
Uma bomba injetora em linha, acima (foto: Panoha/Wikipedia), e um esquema da bomba rotativa, à direita (ilustração: Hydrowatt)
Até meados da década de 1980, o início da injeção (que podemos correlacionar com o avanço de ignição dos motores Otto) e a quantidade de combustível injetado eram controlados por sistemas mecânicos com bombas injetoras (a exemplo do carburador no Otto). Há ainda diversos motores Diesel com controle mecânico de injeção, como em aplicações agrícolas, marítimas e geradores elétricos. Contudo, normas de emissões cada vez mais severas para veículos e necessidade de redução do consumo de combustível forçaram os fabricantes a migrarem para sistemas de controle eletrônicos.
Um exemplo de sistemas mecânicos de injeção de óleo diesel é a bomba em linha, que segue o princípio de usar um eixo com lobes (semelhante ao comando de válvulas) para determinar o tempo e a duração da injeção na câmara de combustão. Claro, é necessário um sistema que limite a rotação do motor: em caso contrário, não haverá limitação de quanto combustível será injetado.
Por isso, um sistema fundamental na bomba injetora mecânica é o governador. Por meio de um sistema de pesos, braços e molas, que gira em função da rotação do motor, ele limita a rotação do motor e elimina a injeção de diesel ao se atingir a rotação predeterminada. Além disso, o sistema tem a função de acelerador do motor Diesel, ao controlar a injeção de combustível em função da requisição do motorista.
Ha também a bomba rotativa, que depois foi adaptada para operar com controle eletrônico nos veículos de passeio. Em geral usada quando não se requer grande vazão por injeção, a bomba rotativa traz como vantagens menor tamanho, baixo ruído de operação, maior eficiência e capacidade de trabalhar com altas pressões. Seu funcionamento, também conectada ao virabrequim, consiste em movimentar os êmbolos (um para cada injetor) responsáveis por criar um pico de pressão para injeção de combustível, os quais são acionados por excêntricos.
Mas motores Diesel com controle mecânico têm grandes limitações no gerenciamento da injeção em situações nas quais se requer melhor controle do tempo de injeção, da duração e da quantidade de diesel injetada, como na operação a frio e em grande altitude.
Com isso, todos os fabricantes de automóveis e caminhões Diesel foram levados a migrar para sistemas eletrônicos de injeção a fim de atender aos níveis atuais de emissões, desempenho, dirigibilidade, ruído e vibrações. Os alicerces do sistema eletrônico estão no injetor de combustível, cuja abertura/injeção é controlada eletricamente, e no sistema computacional potente.
Próxima parte