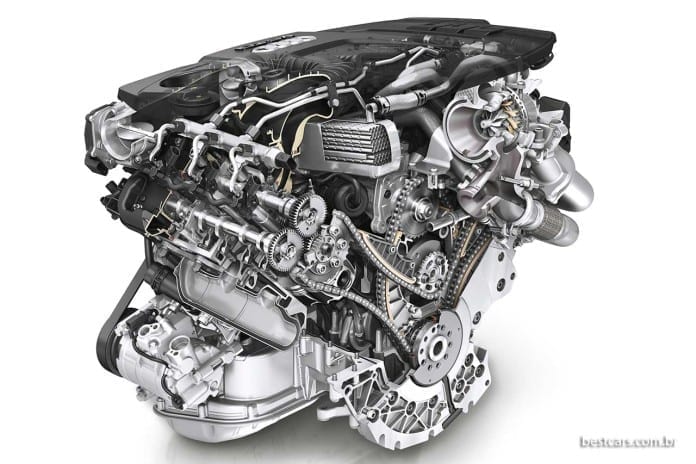
Visto como muito econômico e durável, ele tem características próprias e vem-se desenvolvendo a passos largos
Texto: Felipe Hoffmann – Fotos: divulgação
Bem sucedidos no mercado europeu, desprezados pelos norte-americanos, desejados por muitos brasileiros para seus automóveis, nos quais seu uso é proibido. Trata-se dos motores de ciclo Diesel, que se diferenciam daqueles do ciclo Otto (a gasolina, álcool, flexíveis, a gás natural ou gás liquefeito do petróleo) por muito mais que o combustível que consomem.
O Diesel, desenvolvido no fim do século 19 pelo alemão Rudolf Diesel e oferecido pela primeira vez em um automóvel no Mercedes-Benz 260 D de 1936, ganhou a fama de ser muito econômico e resistente, mas isso ainda se aplica aos motores atuais? E o que se perde com a escolha desse tipo de propulsor?
Das várias características especificas dos motores Diesel, a principal está na autoignição do combustível sem o auxilio de vela de ignição. Nos motores Otto procura-se usar combustível com alta resistência à detonação, qualidade mensurável pela octanagem no caso da gasolina (para o álcool usa-se uma equivalência, embora ele não tenha octanas), pois esse fenômeno é prejudicial ao motor. Do Diesel se espera o oposto, que seja o mais fácil possível detonar. Quanto maior o número de cetanas (CN), mais favorável à autoignição ele será. Vale lembrar que essa característica não está relacionada ao poder calorífico (energia liberada), o qual é semelhante ao da gasolina.
Muitos atribuem o torque limitado em altas rotações aos componentes mais pesados: na verdade, é pela menor velocidade de combustão do diesel
O conceito do motor Diesel é simples. Toda vez que se comprime ar, se aumentam sua pressão e sua temperatura — basta tentar encher um pneu com uma bomba manual e ver como ela esquenta após 10 ou 20 segundos. Agora imagine um motor que comprime o ar 15 a 17 vezes (taxa de compressão) a uma velocidade enorme: é comum atingir temperaturas da ordem de 600⁰C e pressões de 100 bars em motores Diesel turboalimentados durante a fase final de compressão, antes da combustão.
Contudo, o problema está durante a partida a frio, quando a temperatura do motor como um todo e a rotação de partida são baixas — por volta de 100 rpm em motores grandes —, fazendo que parte do ar comprimido literalmente vaze pelos anéis dos pistões. Grandes altitudes também influenciam: o ar menos denso produz menor temperatura na fase final de compressão. O motivo dessa dificuldade está em duas características do óleo diesel, conhecidas como temperatura do ponto de fulgor (temperatura mínima para que se forme vapor suficiente para começar uma chama) e temperatura mínima de ignição.
Combustível | Temperatura do ponto de fulgor (1) | Temperatura mínima de ignição (1) |
Gasolina comum (2) | – 43°C | 300°C |
Gasolina premium (2) | – 43°C | 400°C |
Álcool | 17°C | 420°C |
Diesel | 53°C | 250°C |
Gás natural veicular (GNV) | (3) | 600°C |
Gás liquefeito de petróleo (GLP) | (3) | 400°C |
(1) temperaturas aproximadas; (2) sem álcool; (3) queima em qualquer temperatura por já estar em estado gasoso |
Caso o combustível esteja a uma temperatura abaixo daquela de seu ponto de fulgor, ele não inflama quando se passa uma chama por cima dele ou mesmo se mergulha nele um palito de fósforo. Exemplo típico disso são os motores de injeção indireta (multiponto sequencial, em geral) que usam álcool: com a temperatura de fulgor desse combustível por volta de 17⁰C para o tipo hidratado (no álcool puro, 13⁰C), em dias frios o motor não liga mesmo havendo centelha.
Boa parte do combustível fica presa à válvula de admissão e o pouco vapor que entra no cilindro não tem temperatura suficiente para entrar em ignição. Por isso, ainda não se pode prescindir de sistema de preaquecimento do álcool ou da injeção de gasolina no momento da partida. Já em motores com injeção direta pulveriza-se o álcool durante a fase de compressão, quando o ar está em temperatura muito maior que 17⁰C, o que torna suficiente a combustão com ajuda da centelha.
Combustível | Calor de vaporização (kJ/kg) | Poder calorífico inferior (MJ/kg) | Relação estequiométrica (kg de comb/kg de ar) |
Gasolina comum (1) | 380 a 500 | 41,2 a 41,9 | 14,8 |
Gasolina premium (1) | 380 a 500 | 40,1 a 41,6 | 14,7 |
Álcool | 904 | 25,1 | 8,5 |
Diesel | 250 | 42,9 a 43,1 | 14,5 |
Gás natural veicular (GNV) | (2) | 403 | 14,0 |
Gás liquefeito de petróleo (GLP) | (2) | 46,1 | 15,5 |
(1) sem álcool; (2) já vaporizado em temperatura ambiente |
No motor Diesel, porém, não há centelha e outra característica do combustível se torna importante: a temperatura mínima de ignição. Por outro lado, quanto menor for o calor de vaporização, menos energia o combustível “rouba” do ar para que evapore ou esquente. Ou seja, o ar dentro do cilindro tem de estar a pelo menos 400⁰C para que o óleo diesel atinja sua temperatura mínima (por volta de 250⁰C) e se inicie a combustão. Por isso, em motores Diesel usa-se uma resistência elétrica para partida a frio, a qual é responsável por aquecer o combustível antes de ser injetado no cilindro.
Vale abrir um parêntese. O calor de vaporização é o responsável por motores com álcool produzirem mais potência que com gasolina, uma vez que se necessita de praticamente o dobro de energia para vaporizar o combustível, “esfriando” a câmara de combustão. Isso permite maiores taxas de compressão e avanços de ignição, que beneficiam o desempenho. Junta-se a isso o fato de o álcool trabalhar com menor relação estequiométrica (menos ar para dado volume de combustível) e, no fim, precisa-se de mais de três vezes a energia para evaporar o combustível dentro do cilindro em alta temperatura.
Pode-se dizer então que o álcool “gela” o ar dentro do cilindro, tornando-o mais denso e permitindo mais avanço de ignição (maior eficiência de queima, menor consumo, mais potência). Por isso preparadores de motores gostam muito de passar o motor de gasolina para álcool: o calor “roubado” por ele mantém os cilindros em temperaturas toleráveis para evitar quebras de pistão, sobretudo ao instalar turbocompressor em um motor original de aspiração natural.
Maior torque, menor potência
Voltando ao Diesel, uma vez que a combustão se inicia, o processo se torna uma bola de neve. Quanto mais ciclos de combustão ocorrem, maior a temperatura dentro do cilindro e mais fácil, rápida e completa a queima do combustível. Contudo, há certas características inerentes a esse tipo de motor.
Muitos se perguntam por que motores Diesel fornecem grande torque em baixas rotações, mas obtêm menor potência em altos regimes que os motores Otto. Há dois fatores que influenciam nesse resultado:
1) Motor Diesel não tem problemas com detonação. No motor Otto, muitas vezes o torque é reduzido pela limitação de adiantar o ponto de ignição para obter o maior torque possível, o que o levaria a detonar. Já o Diesel não sofre com essa limitação: seu combustível pode ser injetado no melhor ponto para se obterem os maiores torque e rendimento possíveis naquela rotação e carga (abertura de acelerador). Junta-se a essa característica a alta taxa de compressão e garante-se alto torque — entenda eficiência — em qualquer rotação, o que favorece tanto o torque obtido quanto o consumo de combustível.
O Mercedes 260 D de 1936, primeiro carro de produção a diesel, e seu motor
2) Por ter maior taxa de compressão, necessita-se de maiores inércias de movimento (pode ser o próprio volante do motor) para obter uma rotação de marcha-lenta baixa, bem como baixas vibrações (veja consulta técnica sobre motor “arrastando-se”). Essa característica é percebida quando se está parado e tira-se o pé da embreagem de repente: em vez de o motor apagar, o carro dá um pulo.
Quanto ao torque limitado em altas rotações, muitos acreditam que o principal motivo sejam os pistões e outros componentes mais resistentes e pesados, cujas grandes massas não permitiriam trabalhar em grandes velocidades sem quebras. É claro que esse fator influencia na limitação de giros do motor, mas apenas justificaria a limitação de rotação — não diminuiria o torque em função da rotação.
O principal motivo, na verdade, é a velocidade de combustão ou de frente de chama do óleo diesel, relativamente bem menor que a da gasolina, do álcool ou do gás. Ou seja, quanto mais alta a rotação, menor o período de tempo da fase de combustão. Como exemplo, a 3.000 rpm temos apenas 4 centésimos de segundo (0,04 s) para realizar a combustão em cada ciclo.
Próxima parte
Exemplo de motor Diesel de última geração: o de três cilindros da BMW
Pode-se usar a estratégia de injetar o combustível (ou mesmo realizar a ignição, no caso de motores Otto) durante a fase de compressão, para que a queima ocorra de forma mais eficiente na fase de combustão. No entanto, há um limite físico para esse artifício e, quanto maior for o cilindro, de mais tempo a frente de chama necessitará para percorrer toda a câmara de combustão. Por isso chegou-se a usarem motores na Fórmula 1 com 12 cilindros e cilindrada de 3,0 litros (250 cm³ por cilindro), para que pudessem girar a 18.000 rpm e produzir mais potência (lembre-se da fórmula P = T * rpm, ou potência é igual torque vezes rotação).
Entende-se assim por que é comum um motor Diesel, aplicado a veículos de passeio, obter muito mais torque (com ajuda do turbo), mas potência mais baixa, que no motor a gasolina de mesma cilindrada. Essa vantagem de torque em baixas e médias rotações traz uma maior sensação de desempenho ao motorista. Para melhor entendimento, vamos a gráficos de comparação entre motores Diesel e a gasolina com valores próximos de potência máxima.
Como se pode ver, o torque máximo é bem mais alto no motor Diesel, além de obtido em faixas de rotações mais baixas. Contudo, ambos os motores alcançam potências máximas parecidas, conforme o gráfico abaixo.
Apesar das potências semelhantes (161 cv no Diesel, 152 cv na unidade a gasolina), o Diesel fornece a sensação de desempenho muito superior no uso urbano, pois produz muito mais torque e potência nas faixas mais usadas no dia a dia. Como exemplo, a 2.500 rpm o motor a gasolina tem pouco menos de 75 cv, enquanto o a Diesel já produz cerca de 140 cv. Essa diferença — quase o dobro — traz muito mais agilidade no trânsito ou numa ultrapassagem na qual não seja usada a faixa superior de rotações.
O método carga e o Diesel
Os leitores habituais do Best Cars conhecem o método carga, como chamamos a forma de dirigir que emprega maior abertura de acelerador (carga) e menor rotação para obter o desempenho desejado. Esse método seria válido ao motor Diesel?
Em teoria, sim: por trabalhar sempre com excesso de ar e não ter problemas com detonação, quanto maior a carga (solicitação de torque), maior será a eficiência global do motor. Na prática, porém, tudo depende da situação e da estratégia empregada pelo fabricante. Em alguns casos necessita-se de grande percentual de recirculação de gases (EGR), sobretudo em cargas altas, para reduzir os níveis de óxidos de nitrogênio (NOx — saiba mais no artigo sobre emissões).
No mesmo modelo, em rodovia, o motor Diesel rende por volta de 20% a mais por litro de combustível que um similar a gasolina
Em geral essas regiões de uso do motor não são frequentadas durante os testes-padrão de emissões. Alguns fabricantes então aproveitam essa brecha para não usar EGR nessas situações — afinal, como podem calibrar algo se não houver um limite determinado? Em regra, porém, o método carga pode ser aplicado ao Diesel e trazer boa redução no consumo de combustível. Alguns veículos modernos equipados com transmissão automática têm adotado esse método na calibração da caixa.
Por não haver problema de detonação no motor Diesel, pode-se perseguir sempre o melhor tempo de queima do combustível em cada situação. Já o motor a gasolina pode não estar em seu melhor ponto de ignição para evitar a detonação, o que impacta no rendimento do motor (claro que outros fatores podem influenciar na diferença de rendimento, mas este pode ser considerado o principal motivo).
Para os mesmos motores citados acima, podem ser comparados também os gráficos de consumo específico (medido em gramas por kW a cada hora ou gramas por cv a cada hora) em plena carga, ou seja, com máximo torque:
Nota-se que o motor Diesel obtém consumo específico em média 30% menor. Voltando aos gráficos de potência e torque, vemos que o motor a gasolina produz 75 cv a 2.500 rpm. Após algumas contas, obtemos que nessa condição aquele motor consome cerca de 20 litros por hora, enquanto o motor Diesel produz a mesma potência a 1.500 rpm consumindo em torno de 14 l/h. Vale lembrar que consideramos as curvas em condição de máxima carga (torque), na qual o motor a gasolina tem a grande desvantagem de trabalhar com mistura rica, o que aumenta o consumo (leia em artigo anterior sobre motores).
De posse dos dados em cargas parciais, poderíamos comparar o consumo do mesmo modelo, trafegando em rodovia, com o motor Diesel e outro a gasolina. Em média, com os motores atuais, tem-se uma vantagem por volta de 20% para o motor Diesel nessa condição, na qual o motor a gasolina estaria trabalhando com lambda 1.
Mas como injetar diesel na câmara de combustão na quantidade e no tempo certos?
Uma bomba injetora em linha, acima (foto: Panoha/Wikipedia), e um esquema da bomba rotativa, à direita (ilustração: Hydrowatt)
Até meados da década de 1980, o início da injeção (que podemos correlacionar com o avanço de ignição dos motores Otto) e a quantidade de combustível injetado eram controlados por sistemas mecânicos com bombas injetoras (a exemplo do carburador no Otto). Há ainda diversos motores Diesel com controle mecânico de injeção, como em aplicações agrícolas, marítimas e geradores elétricos. Contudo, normas de emissões cada vez mais severas para veículos e necessidade de redução do consumo de combustível forçaram os fabricantes a migrarem para sistemas de controle eletrônicos.
Um exemplo de sistemas mecânicos de injeção de óleo diesel é a bomba em linha, que segue o princípio de usar um eixo com lobes (semelhante ao comando de válvulas) para determinar o tempo e a duração da injeção na câmara de combustão. Claro, é necessário um sistema que limite a rotação do motor: em caso contrário, não haverá limitação de quanto combustível será injetado.
Por isso, um sistema fundamental na bomba injetora mecânica é o governador. Por meio de um sistema de pesos, braços e molas, que gira em função da rotação do motor, ele limita a rotação do motor e elimina a injeção de diesel ao se atingir a rotação predeterminada. Além disso, o sistema tem a função de acelerador do motor Diesel, ao controlar a injeção de combustível em função da requisição do motorista.
Ha também a bomba rotativa, que depois foi adaptada para operar com controle eletrônico nos veículos de passeio. Em geral usada quando não se requer grande vazão por injeção, a bomba rotativa traz como vantagens menor tamanho, baixo ruído de operação, maior eficiência e capacidade de trabalhar com altas pressões. Seu funcionamento, também conectada ao virabrequim, consiste em movimentar os êmbolos (um para cada injetor) responsáveis por criar um pico de pressão para injeção de combustível, os quais são acionados por excêntricos.
Mas motores Diesel com controle mecânico têm grandes limitações no gerenciamento da injeção em situações nas quais se requer melhor controle do tempo de injeção, da duração e da quantidade de diesel injetada, como na operação a frio e em grande altitude.
Com isso, todos os fabricantes de automóveis e caminhões Diesel foram levados a migrar para sistemas eletrônicos de injeção a fim de atender aos níveis atuais de emissões, desempenho, dirigibilidade, ruído e vibrações. Os alicerces do sistema eletrônico estão no injetor de combustível, cuja abertura/injeção é controlada eletricamente, e no sistema computacional potente.
Próxima parte
Componentes da injeção de duto único, regra hoje em automóveis e utilitários
A injeção de duto único
O sistema de injeção de óleo diesel conhecido por injeção de duto único (em inglês, common rail) é hoje o mais empregado em automóveis e utilitários. Sua principal vantagem é a habilidade de variar o tempo e a pressão de injeção em larga escala, o que permite grandes variações de utilização do motor. É por isso que hoje temos motores Diesel com quase 100 cv/litro de potência específica, embora pequenos em cilindrada: ou seja, baixa injeção requerida de óleo diesel em marcha-lenta e vazão muito alta em potencia máxima.
Isso foi obtido ao separar a pressão e o tempo de injeção. O duto não passa de um acumulador de combustível pressurizado para os injetores — grosso modo, semelhante aos sistemas de injeção indireta dos motores Otto, com sua flauta na qual os injetores se alimentam. A maior diferença está na grande variação de pressão nos motores Diesel, de 200 a 2.200 bars. Além disso, separar a pressurização do controle de injeção permite controle preciso e rápido dos injetores, podendo-se ter até seis injeções de combustível num só ciclo de combustão.
Em geral, em automóveis e comerciais leves, divide-se o sistema de combustível em duas partes: baixa pressão e alta pressão. O de baixa pressão nada mais é que o sistema de combustível do motor Otto adaptado ao Diesel: há uma bomba elétrica de baixa pressão dentro do tanque, a qual é responsável por garantir grande vazão de combustível (até 190 litros por hora) em uma pressão baixa, mas constante (em torno de 6 bars), na entrada da bomba de combustível mecânica.
Em veículos comerciais pesados, que demandam maior vazão (ate 400 l/h), usam-se bombas do tipo engrenagem, em geral integradas à bomba de alta pressão, o que permite a sucção do combustível que está no tanque a certos metros de distância do motor. No fim, o conceito é o mesmo: garantir alta e constante vazão de óleo diesel na entrada da bomba de alta pressão.
Já a bomba de alta pressão, em geral do tipo rotativa (mas pode ser em linha, em alguns veículos comerciais pesados), é responsável por manter pressurizado o duto único, que será o reservatório de combustível pressurizado para os injetores. A pressão desse duto é determinada e controlada pela central eletrônica em função da demanda, por meio de válvulas que podem atuar tanto na saída do duto (ou seja, controlando a pressão pelo lado de alta pressão) quanto na entrada da bomba de alta pressão, antes da pressurização.
A vantagem do controle pelo lado de alta pressão é o tempo de resposta quando há grande variação da carga pelo motorista, caso de uma ultrapassagem. Por outro lado, desperdiça-se energia pressurizando o diesel em momentos de baixa carga, o que impacta o consumo e aquece o combustível a ponto de, muitas vezes, se precisar de um resfriador (como um radiador) de combustível antes que o excesso não usado retorne para o tanque. Afinal, sempre se garante um excesso de vazão na alimentação do duto para não haver risco de falta de combustível nos injetores.
Já controlando a pressão pela entrada da bomba de alta pressão, cria-se um retardo de resposta em grandes variações de carga, mas se economiza combustível. Há ainda estratégias que integram os dois sistemas para conseguir o melhor dos dois mundos.
O borrifo de um injetor limpo, que se perde em grande parte com depósitos
Um borrifo de pequenas gotas
Apesar de o óleo diesel entrar em combustão ao ter contato com o ar comprimido e aquecido, sem auxilio de centelha, isso não significa que basta “derramar” diesel para dentro da câmara de combustão. As altas pressões de injeção foram adotadas, sobretudo, por permitir melhor pulverização do diesel dentro da câmara, formando um borrifo de pequeninas gotas. Afinal, qualquer combustível só queima ao ter contato direto com o oxigênio e, quanto maior a gota, mais combustível ficará “preso” dentro dela sem ter contato com oxigênio.
Tal volume será “liberado” somente quando o combustível da camada externa queimar, deixando para trás um ar pobre em oxigênio que dificultará sua queima completa. Essa é a razão para se verem muitos veículos Diesel sem manutenção adequada soltando fumaça preta. Nesses casos os injetores estão parcialmente entupidos, com desgaste ou funcionamento irregular (muitas vezes por depósitos), fazendo com que o borrifo seja menos vaporizado e mais “jorrado”. Isso dificulta a queima completa, que produz gás carbônico (CO2), e leva a mais emissões de monóxido de carbono (CO) e material particulado (C, carbono).
As altas pressões de injeção visam à melhor pulverização do diesel: quanto maior a gota, mais combustível fica sem contato com oxigênio
Por outro lado, não se podem ter gotas muito pequenas: nesse caso o diesel injetado não atingiria grandes distâncias dentro da câmara, queimando longo no início, o que dificultaria a queima das moléculas que estivessem logo atrás devido à falta de oxigênio. Por isso, estudos minuciosos de turbulência e vórtices criados dentro do cilindro são de grande importância, pois garantem o melhor contato entre o diesel e o oxigênio.
Não se deve esquecer que diversos mecanismos responsáveis por aperfeiçoar a eficiência em motores Otto também atuam nos motores Diesel, como a variação do tempo de abertura das válvulas e o turbocompressor. Há pelo menos 20 anos não se veem mais motores Diesel em veículos, nos principais mercados, sem o uso de turbo.
Além de garantir maior potência específica por meio do aumento de torque (há limitação física do combustível para ganhar potência mediante aumento de rotação), o turbo permite que os motores Diesel modernos atendam a normas cada vez mais restritas de emissões, pois a câmara com maior pressão queima o combustível de maneira mais rápida e eficiente. Pode-se também usar um motor de menor cilindrada para produzir a mesma potência.
Característica da queima do combustível com um só jato pelo injetor na fase de combustão
As estratégias da eficiência
Uma vez entendido como o sistema funciona e quais suas capacidades, como estabelecer estratégias de controle da injeção para melhor eficiência e menores emissões?
O princípio de funcionamento do controle eletrônico não é muito diferente do usado em motores Otto. A central eletrônica recebe dos sensores dados como posição de pedal do acelerador, rotação e posição do virabrequim, pressão e temperatura do ar de admissão, temperatura do líquido de arrefecimento e do óleo lubrificante, entre outros. Com esses dados a central define os melhores parâmetros (tempo e intervalos de injeção, uso de EGR, pressão do turbo) para atingir o torque requerido via acelerador da maneira mais eficiente possível, em termos de consumo e emissões.
Algumas dessas estratégias são tão complexas que fica difícil imaginar como o sistema é capaz. Uma delas é adotada durante o uso normal do veículo para tentar descobrir, com precisão, quanto combustível está sendo injetado em função do tempo de injeção. Lembre-se: tempos de injeção são medidos em milissegundos, e as frações injetadas, em miligramas. Além disso, o tempo de resposta de um injetor de diesel atual está por volta de 150 microssegundos (milionésimos de segundo).
Com pequena variação na rotação do motor (um sinal muito preciso e com alta resolução) e variações do sensor de oxigênio, em combinação ao sensor de massa de ar, o sistema consegue calcular com precisão cirúrgica quanto combustível foi injetado, uma vez que dentro da central eletrônica se conhece a inércia total do motor. Esse procedimento é feito pela central na fase de desaceleração, quando não há sinal de pedal, de modo imperceptível para os ocupantes.
Sem essas adaptações constantes — necessárias pela variação da qualidade do combustível, bem como o desgaste do motor e de seus componente —, o veículo teria problemas para atender aos limites de emissões atuais, sobretudo de material particulado.
Ha também nos motores Diesel atuais um corpo de borboleta que raramente é usado. Esse tipo de motor nunca teve tal item por trabalhar com o máximo de ar possível, ou seja, mistura pobre. O motivo principal para sua adoção é que, ao desligar o motor, fecha-se a borboleta junto à interrupção da injeção de diesel. Se praticamente não há ar sendo aspirado e comprimido no motor, garante-se o desligamento do motor sem grandes vibrações (quem dirigiu picape com motor Diesel de controle mecânico sabe de que se trata). No artigo sobre emissões mencionamos outras estratégias para reduzi-las, como EGR e injeção de ureia.
Próxima parte
A interação dos tempos e durações de injeção com a turbulência ajuda a distribuir de forma homogênea a energia da combustão
Peculiaridades da calibração
Como já sabemos, as grandes vantagens do motor Diesel são não haver preocupação se vai detonar e poder-se injetar o combustível no melhor momento possível para a queima. Por outro lado, como lado negativo, o óleo diesel tem velocidade de queima bem menor que gasolina, álcool, GNV ou GLP, o que dificulta a operação em rotações maiores, bem como o uso da energia liberada no tempo certo (o ideal seria ter uma geração de pressão repentina e alta logo após o ponto-morto superior na fase de combustão).
Contudo, os sistemas dos motores Diesel atuais são capazes de atenuar essas duas características por meio da capacidade de operar até seis injeções durante a fase de combustão, com o objetivo de aumentar a eficiência de queima do combustível, produzir maior torque e reduzir emissões. Essas injeções fracionadas contribuem também para diminuir o nível de ruído do motor.
Injeções fracionadas permitem melhorar ruídos, combustão e emissões
Esse aumento de eficiência decorre dos seguintes fatores:
• Interação dos tempos e durações de injeção com a turbulência e os vórtices gerados: além de favorecer o contato do diesel com a maior quantidade de oxigênio possível, ajuda a distribuir de forma homogênea a energia (calor e pressão) obtida pela combustão.
• Pequena injeção inicial, antes, mas próximo ao ponto-morto superior (durante a fase final de compressão), traz aumento considerável na pressão e na temperatura dentro do cilindro, o que garante uma combustão mais veloz e completa da injeção principal (ou das injeções principais) de diesel durante a fase inicial de combustão.
• Pequena injeção final, no fim da fase de combustão, para que a temperatura dentro do cilindro não caia muito. Se isso ocorrer, favorece a queima incompleta do diesel, que eleva as emissões de hidrocarbonetos (HC). A medida resulta ainda em maior temperatura dos gases de escapamento, ideal para o melhor funcionamento do catalisador. Mas cabe cuidado com essa estratégia: se muito atrasada, pode haver contaminação do óleo do motor por diesel não queimado dentro do cilindro.
Outro fator que limita a potência é que, quanto mais perto da relação estequiométrica, maior a chance de formar material particulado
Como os motores Diesel estão sempre admitindo quantidades máximas de ar, eles necessitam de mais tempo para que o líquido de arrefecimento e o óleo lubrificante atinjam suas temperaturas ideais de trabalho, o que pode agravar a contaminação do óleo pelo combustível. Além disso, em uso normal a temperatura do catalisador é bem mais baixa que em motores Otto.
Isso pode ser uma vantagem sob plena carga (exigindo o máximo de torque e/ou potência) pois, ao contrário do Otto, não há como resfriar os gases de escapamento ou o interior dos cilindros com excesso de combustível. Quanto mais óleo diesel se injeta, maior a temperatura interna dos cilindros e dos gases de escapamento, a ponto de muitos motores Diesel terem sua potência máxima “estrangulada” para proteger peças como pistões e catalisador.
Outro fator que muitas vezes limita a potência máxima do motor Diesel é que, quanto mais perto da relação estequiométrica, maior a chance de formação de material particulado. A questão chega a ponto de produzir fumaça preta, comum em veículos Diesel antigos ao se requisitar mais torque/potência ou durante a variação repentina de carga. Exemplo dessa situação é o veículo estar em uma longa descida, engrenado, e de repente o motorista solicitar rapidamente um alto torque, injetando grande quantidade de diesel com os cilindros “frios” devido ao tempo que se ficou sem acelerar.
As centrais eletrônicas atuais adotam estratégias bastante complexas para evitar a formação de fumaça preta, uma exigência das legislações de emissões atuais. Isso muitas vezes implica um retardo de resposta ao acelerador, dando a impressão de que é o turbo que responde lentamente (turbo lag). Para melhor entender, imagine que o motorista de uma picape roda em baixa velocidade, com motor próximo da marcha-lenta (no caso de caixa manual) ou parado (transmissão automática).
De repente ele crava o pé no acelerador para ter uma resposta tão rápida quanto possível. O que acontece nesse momento?
A câmara de combustão está em baixa temperatura, admitindo pouco ar devido à baixa rotação. Caso a central injete muito combustível, pode chegar perto da relação estequiométrica ou injetar uma quantidade que não conseguirá queima completa devido à baixa temperatura — o resultado será uma bola de fumaça preta na saída do escapamento. Para evitar essa situação a central analisa a massa de ar admitido, a variação da rotação do motor, a temperatura dos gases de escapamento e outros parâmetros para determinar o que se pode traduzir como “curva de crescimento do tempo de injeção”.
Isso significa que, em vez de injetar subitamente todo o diesel requerido, a central determina a injeção progressiva. Mas uma estratégia muito conservadora cria um tempo de resposta muito alto, que afeta a dirigibilidade e a sensação de desempenho do veículo. Por isso, turbinas de geometria variável, de tamanho reduzido ou mesmo dois turbos (sendo um deles pequeno para diminuir o tempo de resposta) são tão aplicados aos motores Diesel.
Pode-se dizer que o retardo do turbo acaba sendo multiplicado pela estratégia de evitar fumaça preta. Assim, quanto mais rápido o turbo “encher”, mais rápido se terá uma grande massa de ar dentro dos cilindros e menor será o tempo de resposta. Essa situação típica de motores Diesel modernos se agrava muito em grandes altitudes, onde o ar rarefeito aumenta o tempo de resposta do turbo. Veículos com caixa automática conseguem atenuar esse fenômeno com o uso de conversores de torque mais “soltos” (velocidade de estol mais alta), mas isso fica para um futuro artigo sobre transmissão.
A turbina de geometria variável contribui para menor tempo de resposta e mais agilidade
Se custo não for problema, há soluções como a do novo Audi SQ7, que usa um compressor elétrico junto aos turbos. Com resposta quase que imediata ao acelerador, o compressor elétrico enche rapidamente os cilindros de ar pressurizado, de forma a eliminar o retardo dos turbos em rotações baixas. Afinal, quem compra um carro como esse não quer ficar para trás em relação a carros “comuns” em uma saída de semáforo com mais vigor… É comum demorar até 2 s — uma eternidade quando se requer agilidade, como ao acessar uma via de alta velocidade — para se obter o torque máximo em motores Diesel.
Outra estratégia interessante para economizar óleo diesel, mas delicada para evitar fumaça preta, é reduzir ou eliminar a pressão de turbo em velocidades e acelerações moderadas, nas quais não se precisa de tanta pressão para produzir o torque necessário. As vantagens dessa estratégia estão em diminuir as perdas por bombeamento (quanto mais ar na admissão, mais energia se gasta na fase de compressão) e poder reduzir o uso de EGR, que em geral prejudica a eficiência do motor. Afinal, maior pressão de admissão significa maior temperatura nos cilindros e, em consequência, maior produção de óxidos de nitrogênio (NOx).
Por outro lado, as desvantagens são um pouco de retardo na resposta ao acelerador — sobretudo por causa da estratégia que evita fumaça preta — e probabilidade de maiores emissões de HC e CO (monóxido de carbono). O balanço ideal deve ser bem definido para que o tiro não saia pela culatra: além dos aspectos legais, nenhum consumidor gosta de ver seu carro novo soltando fumaça preta.
À primeira vista os motores Diesel parecem ser mais simples que os motores Otto, por não necessitarem de centelha e de todo o sistema de ignição. Contudo, as exigências cada vez maiores, tanto pelos órgãos regulatórios (emissões) quanto pelo consumidor (alta potência e baixos consumo, vibrações e ruídos), forçaram os motores Diesel a um elevado nível de complexidade, com impacto nos custos de peças e sistemas eletrônicos e crescentes desafios à engenharia de desenvolvimento.
Mais Técnica
Durabilidade: verdade ou mito?
Mas isso se deve aos critérios de projeto do motor e não a ser um Diesel. Hoje, em aplicações de automóveis e utilitários leves, pode-se dizer que a durabilidade dos motores Diesel não difere muito da obtida pelos motores Otto. Afinal, não importando o tipo de motor ou de combustível, ambos precisam passar pelos mesmos testes de durabilidade exigidos por cada fabricante.
O fato de diversas partes do sistema de combustível serem lubrificadas pelo próprio óleo diesel, além de operarem com folgas reduzidas e pressões elevadas, faz que os motores Diesel sejam mais sensíveis a impurezas presentes no combustível. Além disso, a água presente no óleo diesel pode criar pontos de oxidação e comprometer peças vitais das bombas e injetores. Por isso veículos Diesel possuem sistemas de filtros robustos e, em alguns modelos, sistema integrado de separação de água do combustível.